Selecting the Right Trim for Gate Valves in Petrochemical and Pulp Mill Processes
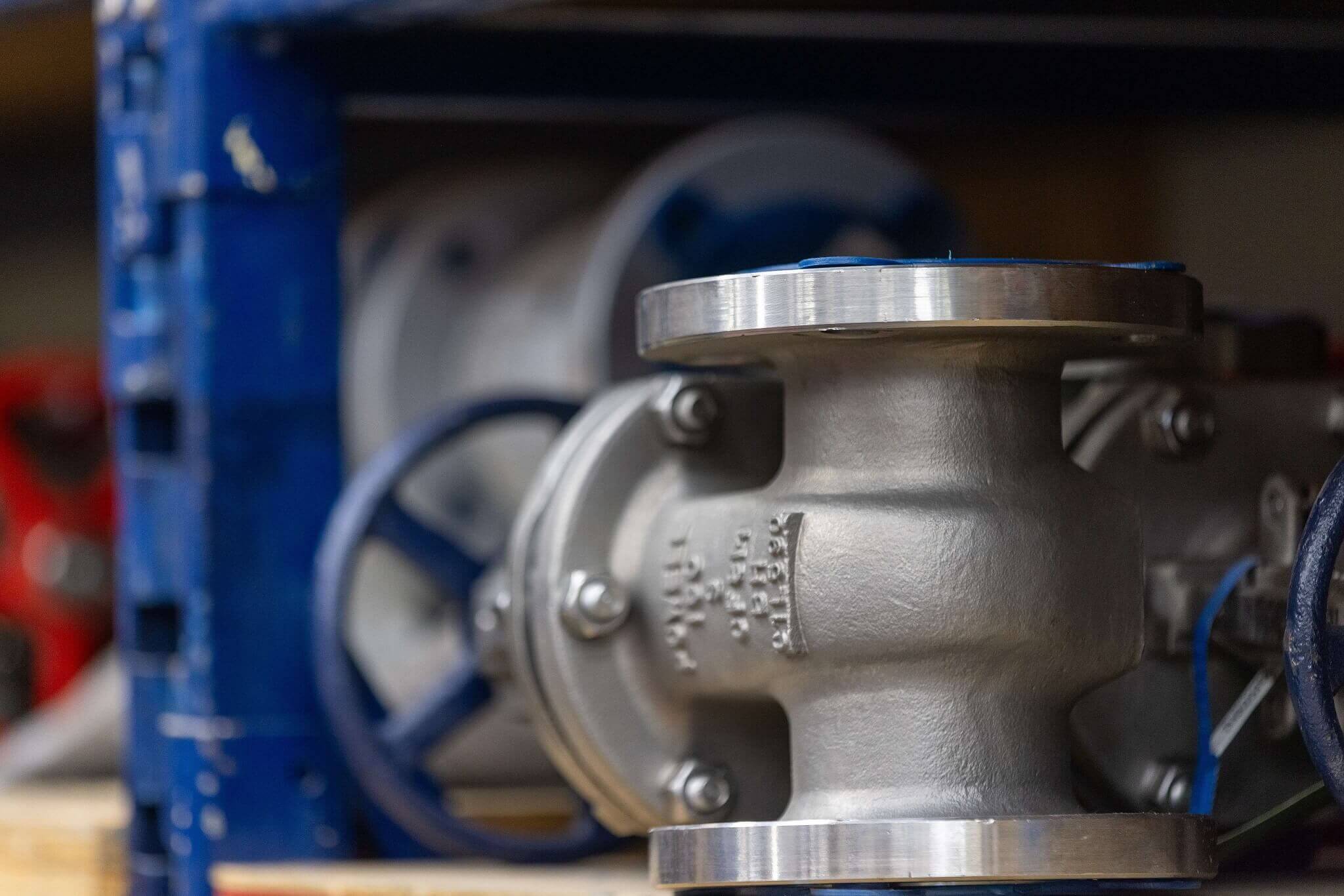
In the petrochemical and pulp mill industries, gate valves play a crucial role in controlling the flow of fluids and slurries. The selection of the correct trim for these valves is essential, as it directly impacts operational efficiency, safety, and maintenance costs. The trim, which includes the valve’s internal components such as the disc, seat, and stem, must be tailored to the specific characteristics of the media being handled. Different processes can involve aggressive chemicals, high temperatures, and varying pressures, necessitating careful consideration of material compatibility and design features.
One of the primary considerations in trim selection is the chemical compatibility of materials. In petrochemical processes, for instance, corrosive substances can rapidly degrade valve components if not carefully chosen. Using trims made from corrosion-resistant materials, such as stainless steel or specialized alloys, ensures longevity and reduces the risk of leaks or failures that could result in costly downtime or environmental hazards. Similarly, in pulp mills, where abrasive slurries are common, selecting a trim that can withstand wear is vital to maintaining performance and reducing the frequency of maintenance interventions.
Another critical factor is the operating conditions, including temperature and pressure. Gate valves are often employed in high-pressure environments, where the integrity of the trim must be guaranteed to prevent catastrophic failures. High-temperature applications may require trims that can endure thermal expansion without compromising sealing capabilities. Selecting the appropriate trim based on these parameters not only enhances valve performance but also contributes to overall system reliability, which is particularly important in industries where unplanned outages can lead to significant financial losses.
Finally, the long-term cost implications of trim selection cannot be overlooked. While it might be tempting to opt for lower-cost materials or standard designs, investing in high-quality trims specifically suited for the application can lead to substantial savings over time. Improved durability translates to fewer replacements, reduced maintenance costs, and minimal risk of operational interruptions. By prioritizing the correct trim selection, companies in the petrochemical and pulp mill sectors can optimize their processes, enhance safety, and ensure efficient resource management.