Hydraulic Thread Connections: A Guide to Choosing the Right Fitting
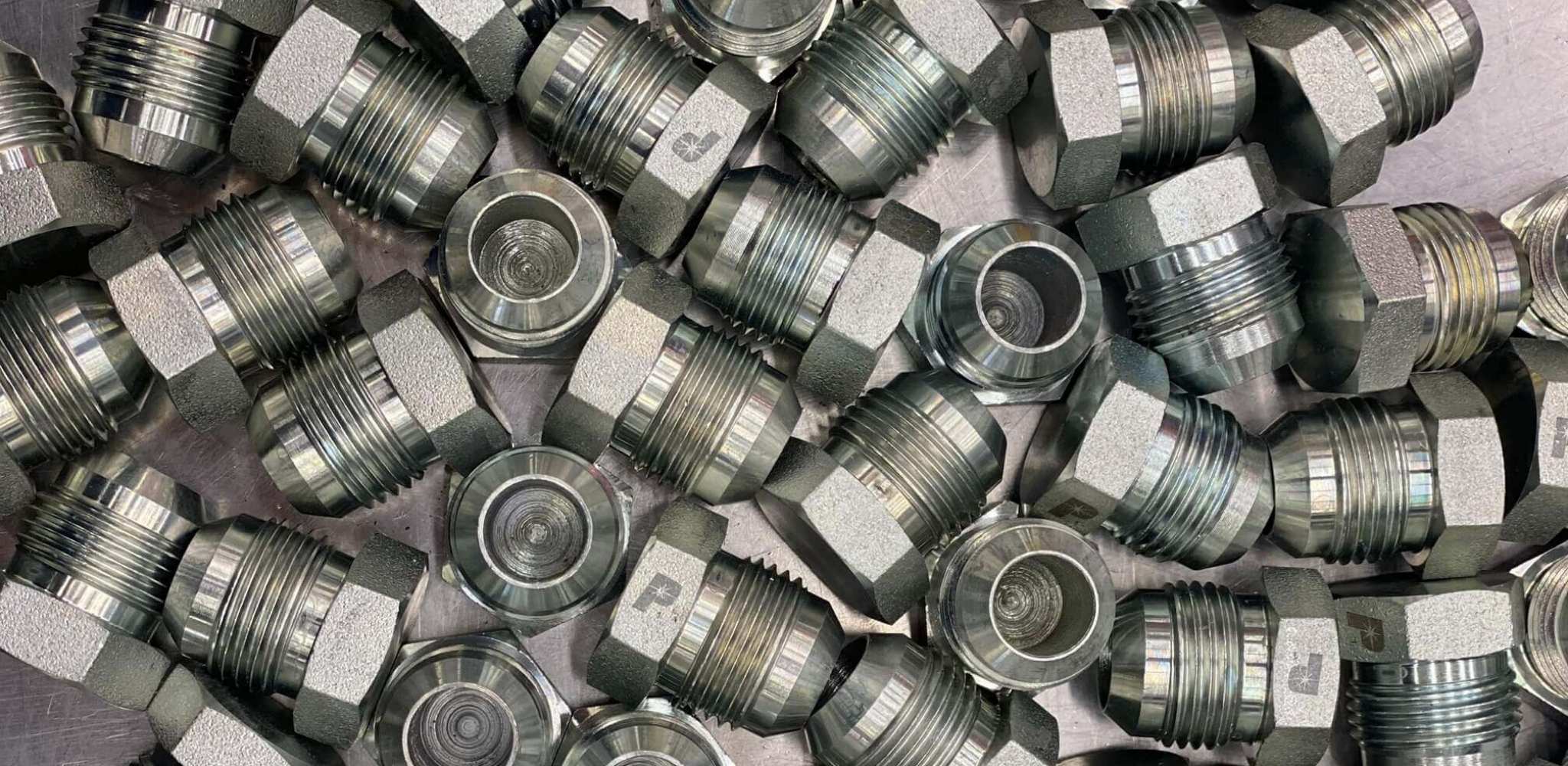
Hydraulic systems are fundamental to a wide range of industries, from heavy machinery and processing facilities to automotive and manufacturing. These high-pressure fluid networks power critical functions like lifting, lowering, braking, and steering, making reliable connections an essential component. Improper or failing hydraulic fittings can lead to costly downtime, equipment damage, and even safety hazards. Understanding the key differences between common hydraulic thread types – including JIC, ORFS, ORB, NPT, Code 61/62, and DIN – is crucial for selecting the right connection for each application and maintaining optimal system performance.
One of the most widely used hydraulic thread connections is JIC (Joint Industry Council), also known as 37° flare. JIC fittings feature a 37-degree taper on the male end that forms a seal when tightened against a corresponding female flare. JIC connections are widely popular across industries like agriculture, construction, and manufacturing due to their widespread availability, relatively low cost, and ease of assembly. Their simple design and wide acceptance make JIC fittings a go-to choice for many hydraulic applications. However, the flared sealing surfaces can be susceptible to leaks if the mating components become worn or damaged over time, especially in harsh environments. This requires periodic inspection and maintenance to ensure continued reliability.
In contrast, ORFS (O-Ring Face Seal) connections uses an O-ring seal rather than a flare. The male fitting has a flat face with an O-ring groove, which compresses against a flat face on the female fitting when tightened. ORFS fittings offer superior sealing performance and can withstand significantly higher pressures than JIC, making them a popular choice for mobile equipment, machinery, and other applications requiring robust, high-pressure hydraulic systems. Their O-ring seals provides enhanced leak prevention, but these fittings generally cost more, and the seal is susceptible to cracks and failures leading to downtime and added maintenance.
ORB (O-Ring Boss) fittings use a similar sealing mechanism to ORFS, but with an O-ring at the base of the threads rather than the face of the fitting. When tightened, this O-ring is compressed into a chamfer when mating the male and female connections, creating a tight seal. This allows for a more compact and adaptable connection, which is advantageous in space-constrained hydraulic systems like those found in agricultural, construction, and forestry. The threaded design also provides a more secure connection compared to the flared JIC fittings. However, ORB connections have a slightly lower pressure capacity than ORFS, making them better suited for medium-duty applications.
For easier installation, NPT (National Pipe Taper) fittings are a common choice. NPT threads create a seal through the mating of the male and female tapered threads. NPT connections are inexpensive, easy to assemble, and widely available, which has contributed to their widespread use in industrial, automotive, and plumbing applications. However, they can be prone to leaks if not properly tightened or if the threads become damaged over time, requiring more frequent inspection and maintenance compared to other hydraulic thread types.
Code 61, Code 62 and Caterpillar flanges work in conjunction with four-bolt flange kits to create a leak-free connection and are often used in high-pressure applications when using tubing or pipe. The male flange has a recessed groove for an O-ring that is compressed against a flat service and the O-ring head when the fasteners of the flange kits are tightened. Code 61 flanges have pressure capabilities up to 5000 PSI, whereas Code 62 and Caterpillar flanges are rated for 6000 PSI, and are the preferred fitting for industries such as heavy machinery, mobile equipment, and other demanding applications that require a more robust working capacity.
Previously only found in Europe, the DIN (Deutsche Industrie Normen, which translate to German Industrial Standard) is gaining increasingly more popularity in North America. This hydraulic thread system is widely used across a variety of industries including mining, steel production, and farming. DIN fittings incorporate a 24-degree taper and uses a combination of threads and an O-ring or spherical nose for sealing. This design is known for its robustness and versatility and ease of use between adapters and hydraulic tubing.
Choosing the appropriate hydraulic thread connection is crucial for ensuring the safe and reliable operation of any pressurized fluid system. Improper fittings can lead to costly leaks, equipment damage, and even safety hazards in the workplace. Each connection type offers unique strengths and limitations in terms of pressure rating, sealing performance, installation complexity, and cost. Carefully evaluating the specific requirements of your application – whether it’s heavy industrial machinery, mobile equipment, or aerospace components – is essential for selecting fittings that will maintain leak-free operation and protect personnel from the dangers of pressurized fluid release. Taking the time to understand the trade-offs between common hydraulic thread standards can pay dividends in terms of minimizing downtime and preserving the safety of your hydraulic systems.