Understanding ANSI Flanges
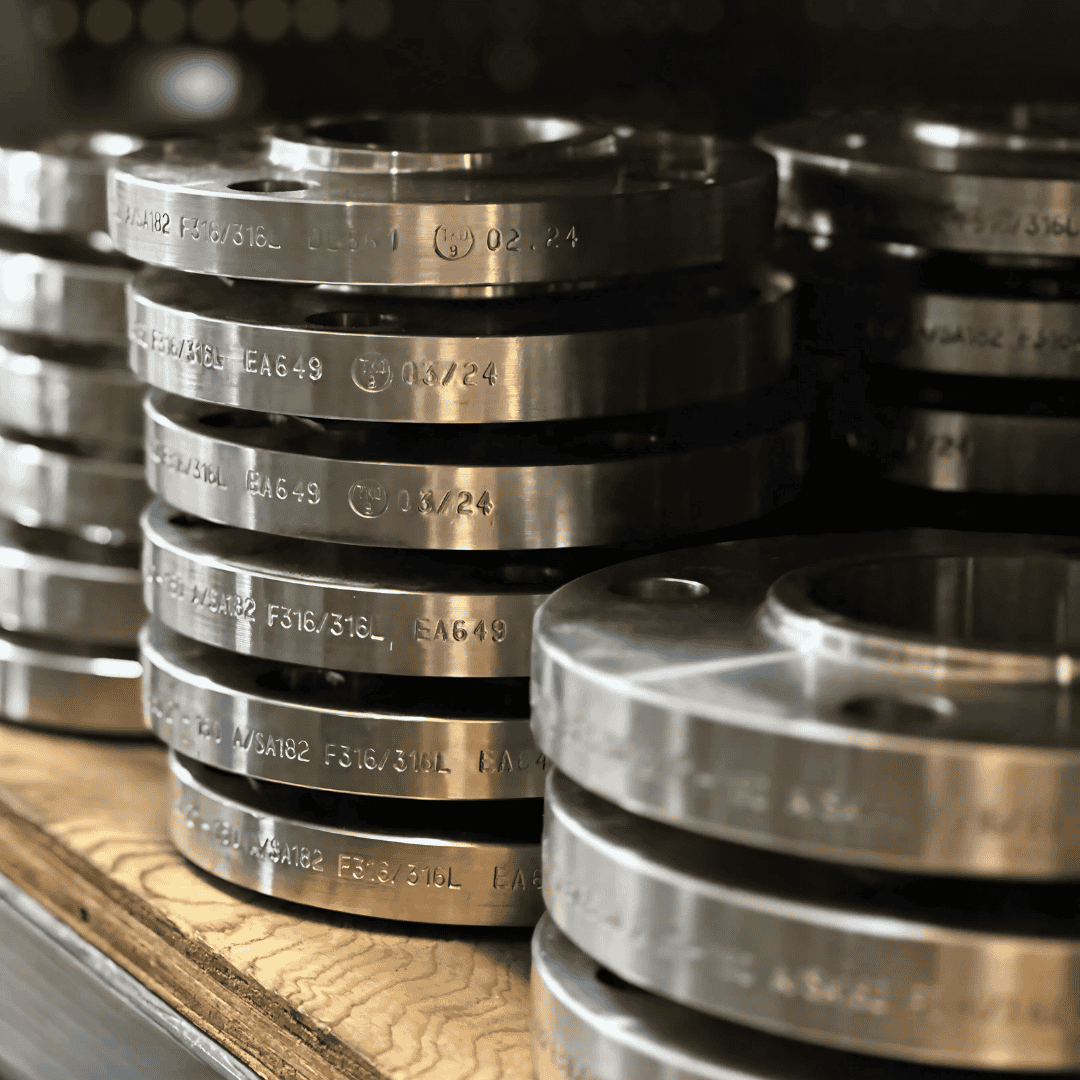
Flanges play a critical role in piping systems, connecting pipes, valves, pumps, and other equipment to form sealed and secure assemblies. ANSI (American National Standards Institute) flanges are widely used in industrial settings due to their standardized specifications, ensuring compatibility and safety in diverse applications. Each type of flange offers distinct advantages depending on the requirements of the system. The eight most common types of ANSI flanges include threaded, weld-neck, slip-on, socket-weld, blind, lap-joint, Vanstone, and RTJ flanges.
Threaded Flanges
Threaded flanges, also known as screwed flanges, are designed with threads that allow them to be screwed onto a pipe without the need for welding. This feature makes them ideal for low-pressure and low-temperature applications, as well as systems where welding is impractical or dangerous. These flanges are easy to install and remove, making them suitable for maintenance-heavy environments. However, threaded flanges are not recommended for high-pressure or high-vibration situations, as the threads can loosen over time.
Weld-Neck Flanges
Weld-neck flanges are characterized by their long-tapered hub, which is welded to the pipe. This design provides excellent stress distribution, making these flanges ideal for high-pressure, high-temperature applications where safety and durability are paramount. The gradual transition from the flange to the pipe minimizes stress concentration at the base of the flange, reducing the likelihood of fatigue failure. Weld-neck flanges are commonly found in industries such as oil and gas, chemical processing, and power generation.
Slip-On Flanges
Slip-on flanges are designed to slide over the outside of a pipe and are then welded in place. They are easy to install and align, making them a popular choice for low-pressure applications where speed and convenience are important. The lower initial cost compared to weld-neck flanges makes slip-on flanges a cost-effective solution for many projects. However, since they require both a fillet weld on the inside and outside of the flange, their strength is slightly lower than that of weld-neck flanges.
Socket-Weld Flanges
Socket-weld flanges are similar to slip-on flanges but have a socket inside the flange where the pipe is inserted before being welded in place. This design provides a smooth bore and improved fluid flow within the piping system. Socket-weld flanges are typically used in small-diameter, high-pressure systems where precise alignment is crucial. These flanges are often preferred in applications involving gas or steam, as the internal welding helps prevent leakage and ensures a reliable connection.
Blind Flanges
Blind flanges are solid plates used to block off or close the end of a piping system. They are crucial for systems that may need to be temporarily or permanently shut off. Blind flanges allow for easy access to the piping system for maintenance or expansion in the future. Since they don’t have a bore like other flanges, they can handle high-pressure applications and provide an effective seal, making them popular in industries such as oil and gas, chemical processing, and water treatment.
Lap-Joint Flanges
Lap-joint flanges, often used with stub ends, are designed for situations where frequent disassembly or alignment adjustments are required. The stub end is welded to the pipe, while the lap-joint flange slides over it, remaining free to rotate. This makes bolt alignment easier and reduces wear on the flange during repeated assemblies and disassemblies. Lap-joint flanges are commonly used in low-pressure applications and systems where cost savings are a priority, as the flanges can be reused even if the stub ends need replacing.
Vanstone Flanges
Vanstone flanges, also known as lap-joint flanges (a subset of lap-joint flanges), consist of two components: a stub end and a loose backing flange. The stub end is welded to the pipe, while the backing flange remains free to rotate, allowing easy alignment of bolt holes. Vanstone flanges are particularly useful in systems that require frequent disassembly or adjustments. These flanges are ideal for low-pressure applications where cost savings and flexibility are important.
RTJ (Ring-Type Joint) Flanges
RTJ flanges are designed with a groove that holds a metal ring gasket. When the flanges are bolted together, the gasket is compressed into the groove, creating a leak-proof seal. This makes RTJ flanges ideal for high-pressure, high-temperature applications such as oil and gas, where leakage can have serious consequences. The metal-to-metal seal provided by the ring gasket ensures long-lasting, reliable performance, even under extreme conditions. RTJ flanges are often used in petrochemical plants and offshore platforms where safety is critical.
Conclusion
Each type of ANSI flange offers unique advantages based on the specific requirements of the piping system. From the ease of installation of threaded and slip-on flanges to the high-pressure performance of weld-neck, blind, and RTJ flanges, understanding these differences is key to selecting the right flange for your application. Whether you’re working in construction, oil and gas, or another industrial sector, choosing the correct flange type ensures the safety, durability, and efficiency of your piping system.